The New Industrial Engineering: Information Technology and Business Process Redesign
Those aspiring to improve the way work is done must begin to apply the capabilities of information technology to redesign business processes. Business process design and information technology are natural partners, yet industrial engineers have never fully exploited their relationship. The authors argue, in fact, that it has barely been exploited at all. But the organizations that have used IT to redesign boundary-crossing, customer-driven processes have benefited enormously. This article explains why.
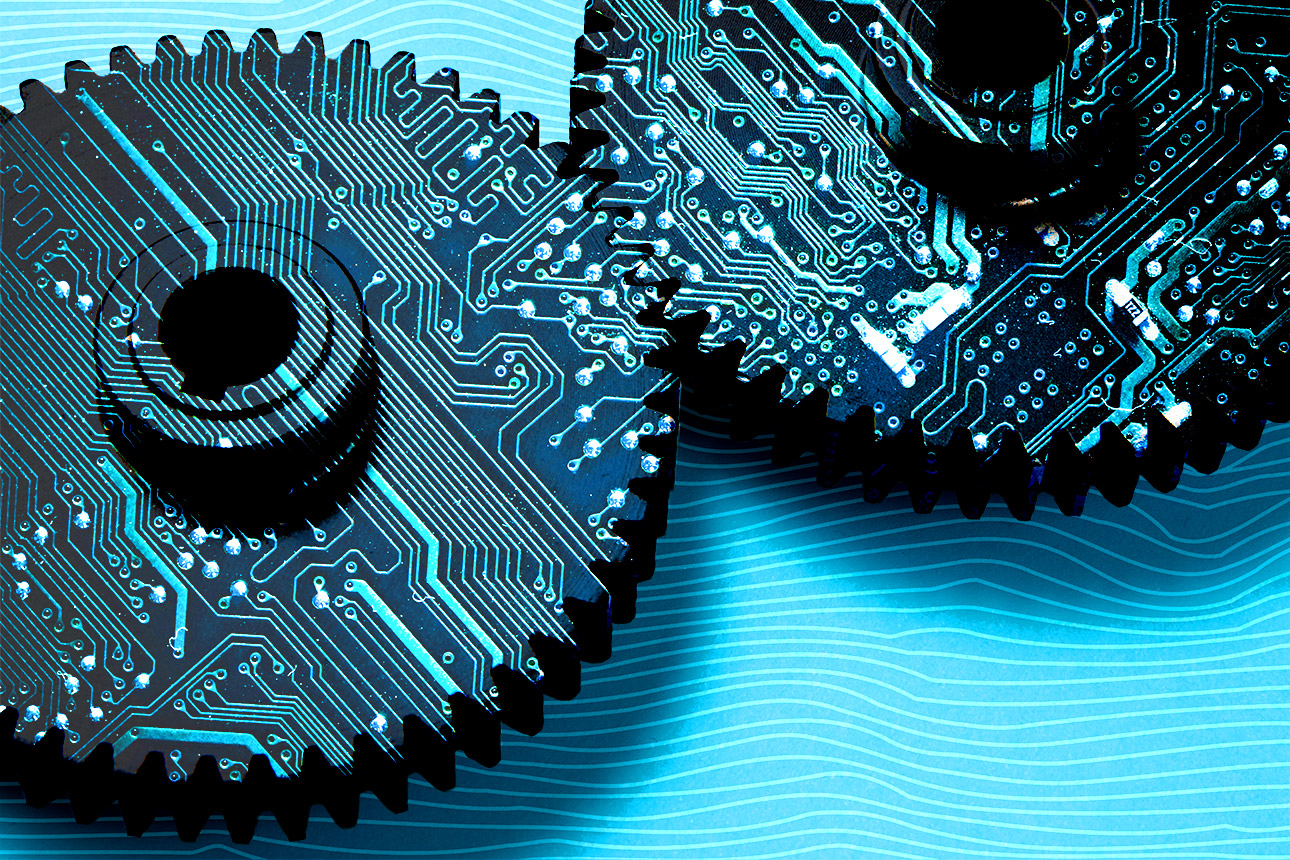
At the turn of the century, Frederick Taylor revolutionized the workplace with his ideas on work organization, task decomposition, and job measurement. Taylor’s basic aim was to increase organizational productivity by applying to human labor the same engineering principles that had proven so successful in solving the technical problems in the work environment. The same approaches that had transformed mechanical activity could also be used to structure jobs performed by people. Taylor came to symbolize the practical realizations in industry that we now call industrial engineering (IE), or the scientific school of management.1 In fact, though work design remains a contemporary IE concern, no subsequent concept or tool has rivaled the power of Taylor’s mechanizing vision.
As we enter the 1990s, however, two newer tools are transforming organizations to the degree that Taylorism once did. These are information technology–the capabilities offered by computers, software applications, and telecommunications–and business process redesign–the analysis and design of work flows and processes within and between organizations. Working together, these tools have the potential to create a new type of industrial engineering, changing the way the discipline is practiced and the skills necessary to practice it.
This article explores the relationship between information technology (IT) and business process redesign (BPR). We report on research conducted at MIT, Harvard, and several consulting organizations on nineteen companies, including detailed studies of five firms engaged in substantial process redesign. After defining business processes, we extract from the experience of the companies studied a generic five-step approach to redesigning processes with IT. We then define the major types of processes, along with the primary role of IT in each type of process. Finally, we consider management issues that arise when IT is used to redesign business processes.
IT in Business Process Redesign
The importance of both information technology and business process redesign is well known to industrial engineers, albeit as largely separate tools for use in specific, limited environments.2 IT is used in industrial engineering as an analysis and modeling tool, and IEs have often taken the lead in applying information technology to manufacturing environments. Well-known uses of IT in manufacturing include process modeling, production scheduling and control, materials management information systems, and logistics.
References
1. L. Gulick, "Notes on the Theory of Organization," in L. Gulick and L. Urwick, eds., Papers on the Science of Administration (New York: Institute of Public Administration, 1937), p. 9.
2. S. Sakamoto, "Process Design Concept: A New Approach to IE," Industrial Engineering, March 1989, p. 31.
3. "Office Automation: Making It Pay Off," Business Week, 12 October 1987, pp. 134–146. For an alternative perspective, see R.E. Kraut, ed., Technology and the Transformation of White-Collar Work (Hillsdale, New Jersey: Lawrence Erlbaum Associates, 1987).
4. G.W. Loveman, "An Assessment of the Productivity Impact of Information Technologies" (Cambridge, Massachusetts: MIT Sloan School of Management, Management in the 1990s, Working Paper 90s:88–054, July 1988). Loveman studied microeconomic data from manufacturing firms to estimate econometrically the productivity impact of IT in the late 1970s and early 1980s. In finding no significant positive productivity impact from IT, he argues that his findings in manufacturing raise serious questions about impacts in nonmanufacturing firms as well.
Baily and Chakrabarti (1988) studied white-collar productivity and IT as one part of a broader inquiry into poor productivity growth. They found no evidence of significant productivity gain. See M.N. Baily and A. Chakrabarti, Innovation and the Productivity Crisis (Washington, D.C.: Brookings Institution, 1988).
5. Loveman (1988); Baily and Chakrabarti (1988). See also L.C. Thurow, "Toward a High-Wage, High-Productivity Service Sector" (Washington, D.C.: Economic Policy Institute, 1989).
6. Robert Horton, who became chairman and chief executive of British Petroleum in March 1990, argues that his major concern in setting BP's course in the next decade is "managing surprise." Horton's belief is that the external business environment is so unpredictable that surprise, rather than managed change, is inevitable. See R. Horton, "Future Challenges to Management," MIT Management, Winter 1989, pp. 3–6.
7. T Malone, "What is Coordination Theory?" (Cambridge, Massachusetts: MIT Sloan School of Management, Center for Coordination Science, Working Paper No. 2051–88, February 1988); K. Crowston and T Malone, "Information Technology and Work Organization" (Cambridge, Massachusetts: MIT Sloan School of Management, Center for Information Systems Research, Working Paper No. 165, December 1987).
8. G.A Pall, Quality Process Management (Englewood Cliffs, New Jersey: Prentice-Hall, 1987). Our definition also complements that of Schein, who focuses on human processes in organizations–e.g., building and maintaining groups, group problem solving and decision making, leading and influencing, etc. See E.H. Schein, Process Consultation: Its Role in Organization Development, Vol. 1, 2d ed. (Reading, Massachusetts: Addison-Wesley, 1988).
9. E.J. Kane, "IBM's Total Quality Improvement System" (Purchase, New York: IBM Corporation, unpublished manuscript), p. 5.
10. See, for example, M.F. Morris and G.W. Vining, "The IE's Future Role in Improving Knowledge Worker Productivity," Industrial Engineering, July 1987, p. 28.
11. "Reference Note on Work Simplification" (Boston: Harvard Business School, HBS Case Services #9-609-0601961, 1961).
12. The relationship between business vision and IT has been explored by several researchers under the auspices of the MIT Sloan School's five-year "Management in the 1990s" research program. An overview volume is scheduled for publication by Oxford University Press in August 1990.
13. See, for example, G. Stalk, Jr., "Time–The Next Source of Strategic Advantage," Harvard Business Review, July–August 1988, pp. 41–51.
14. S. Zuboff, In the Age of the Smart Machine (New York: Basic Books, 1988).
15. E.H. Schein, "Innovative Cultures and Organizations" (Cambridge, Massachusetts: MIT Sloan School of Management, Management in the 1990s, Working Paper 90s:88–064, November 1988).
16. Information engineering and other redesign approaches based on data modeling are necessarily limited in scope. More than data is exchanged in many process relationships. Note too that many companies have used information engineering methods without a specific process orientation.
17. Examples of IT planning approaches where high-impact objectives and/or goals are defined include critical success factors (CSFs) and business systems planning(BSP). See J.F Rockart, "Chief Executives Define Their Own Data Needs," Harvard Business Review, March–April 1979, pp. 81–93; and IBM, Information Systems Planning Guide, 3d ed. (Business Systems Planning Report No. GE20-05527-2, July 1981).
18. D Goodhue, J. Quillard, and J. Rockart, "Managing the Data Resource: A Contingency Perspective" (Cambridge, Massachusetts: MIT Sloan School of Management, Center for Information Systems Research, Working Paper No. 150, January 1987).
19. J.F. Rockart, "The Line Takes the Leadership–IS Management in a Wired Society," Sloan Management Review, Summer 1988, pp. 57–64.
20. J.C. Henderson and N. Venkatraman, "Strategic Alignment: A Process Model for Integrating Information Technology and Business Strategies" (Cambridge, Massachusetts: MIT Sloan School of Management, Center for Information Systems Research, Working Paper No. 196, October 1989).
21. Dorothy Leonard-Barton introduced the concept of organizational prototyping with regard to the implementation of new information technologies. See D Leonard-Barton, "The Case for Integrative Innovation: An Expert System at Digital," Sloan Management Review, Fall 1987, pp. 7–19.
22. R. Johnston and PR. Lawrence, "Beyond Vertical Integration –The Rise of the Value-Adding Partnership," Harvard Business Review, July–August 1988, pp. 94–101. See also N. Venkatraman, "IT-Induced Business Reconfiguration: The New Strategic Management Challenge" (Cambridge, Massachusetts: Paper presented at the annual conference of the MIT Center for Information Systems Research, June 1989).
23. T.J. Main and J.E. Short, "Managing the Merger: Building Partnership through IT Planning at the New Baxter," Management Information Systems Quarterly, December 1989, pp. 469–486.
24. C.R. Hall, M.E. Friesen, and J.E. Short, "The Turnaround at US Sprint: The Role of Improved Partnership between Business and Information Management," in progress.
25. R.R. Johansen, Groupware: Computer Support for Business Teams (New York: The Free Press, 1988). Also see C.V. Bullen and R.R. Johansen, "Groupware: A Key to Managing Business Teams?" (Cambridge, Massachusetts: MIT Sloan School of Management, Center for Information Systems Research, Working Paper No. 169, May 1988).
26. See L.M. Applegate, "The Center for Machine Intelligence: Computer Support for Cooperative Work" (Boston: Harvard Business School Case Study No. 189–135, 1988, rev. 1989).
27. J.E. Ashton and F.X. Cook, "Time to Reform Job Shop Manufacturing," Harvard Business Review, March–April 1989, pp. 106–111.
28. See cases on "Tiger Creek," "Piney Wood," and "Cedar Bluff in S. Zuboff (1988); other industries discussed by Zuboff primarily involve informational processes.
29. One might consider managerial processes synonymous with informational processes. Certainly the vast majority of managerial processes, such as budgeting, planning, and human resource development, involve informational objects. Yet it is important to remember that informational processes can be either operational or managerial, so we believe that this separate dimension of process types is warranted.
30. A case study describes the process and the creation of the expert system. See "Texas Instruments Capital Investment Expert System" (Boston: Harvard Business School Case Study No. 188–050, 1988).
31. Some aspects of this process improvement are described in L.M. Applegate and C.S. Osborne, "Xerox Corporation: Executive Support Systems" (Boston: Harvard Business School Case Study No. 189–134, 1988, rev. 1989).
32. R.H.C. Pugh, address to McKinsey & Co. information technology practice leaders, Munich, Germany, June 1989.
33. See, for example, A.R. Cohen and D.L. Bradford, "Influence without Authority: The Use of Alliances, Reciprocity, and Exchange to Accomplish Work," Organizational Dynamics, Winter 1989, pp. 4–17.
34. See G.A. Pall (1987).