Sensing the Future Before It Occurs
William Ruh, who runs General Electric’s global software headquarters, explains how combining sensors with analytics allows companies to spot potential equipment problems before they occur.
Topics
Competing With Data & Analytics
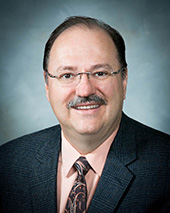
William Ruh, vice president and general corporate officer of General Electric’s global software headquarters
William Ruh is vice president and general corporate officer of General Electric’s global software headquarters, which opened in mid-2012 in San Ramon, Calif.
Ruh says that he never thought he’d work at an industrial company, having spent most of his working life in technology; most recently, he was at Cisco, where he was head of global services and solutions. But he says that General Electric convinced him it was serious about the potential transformative effect of software in industrial environments.
Now Ruh is the point person for GE on its “Industrial Internet” concept, a version of the idea of the Internet of things in which industrial machines connect to other machines and share data that will help companies improve operations. A key to the Industrial Internet is leveraging intelligent sensors in new ways. MIT Sloan Management Review contributing editor on Digital Transformation Michael Fitzgerald talked with Ruh by phone about why intelligent sensors matter.
Why is GE pushing this Industrial Internet now?
Change is coming from two dimensions. There’s the business dimension, because of the economies around the world not seeing huge GDP growth we saw in the past. Most businesses are looking and saying, “if I’m going to meet my financial objectives, I’m not going to count on GDP growth.” You have to complement with greater emphasis on productivity. We call it the One Percent factor. For example, companies use our gas turbines to generate 25% of the world’s electricity. A 1% savings in fuel is worth $4.5 billion. A 1% change they can take to the bank and to shareholders. That’s quite interesting.
The second piece is the technology side. The Internet has driven the ability to connect cheaply and easily and make devices more intelligent. We’re really riding the cell phone industry’s investments and driving down of the price of wireless processing and communications, so we can leverage it on other devices. The second technology shift has been around data and the idea of processing data. Real-time, no SQL, Hadoop and other kinds of big data technologies are actually very early on. They give us hope that we can manage this data differently than we did before.