The Promise of Self-Sufficient Production
As global supply chains have revealed their vulnerabilities during the pandemic, digital fabrication technologies demonstrate a new way forward.
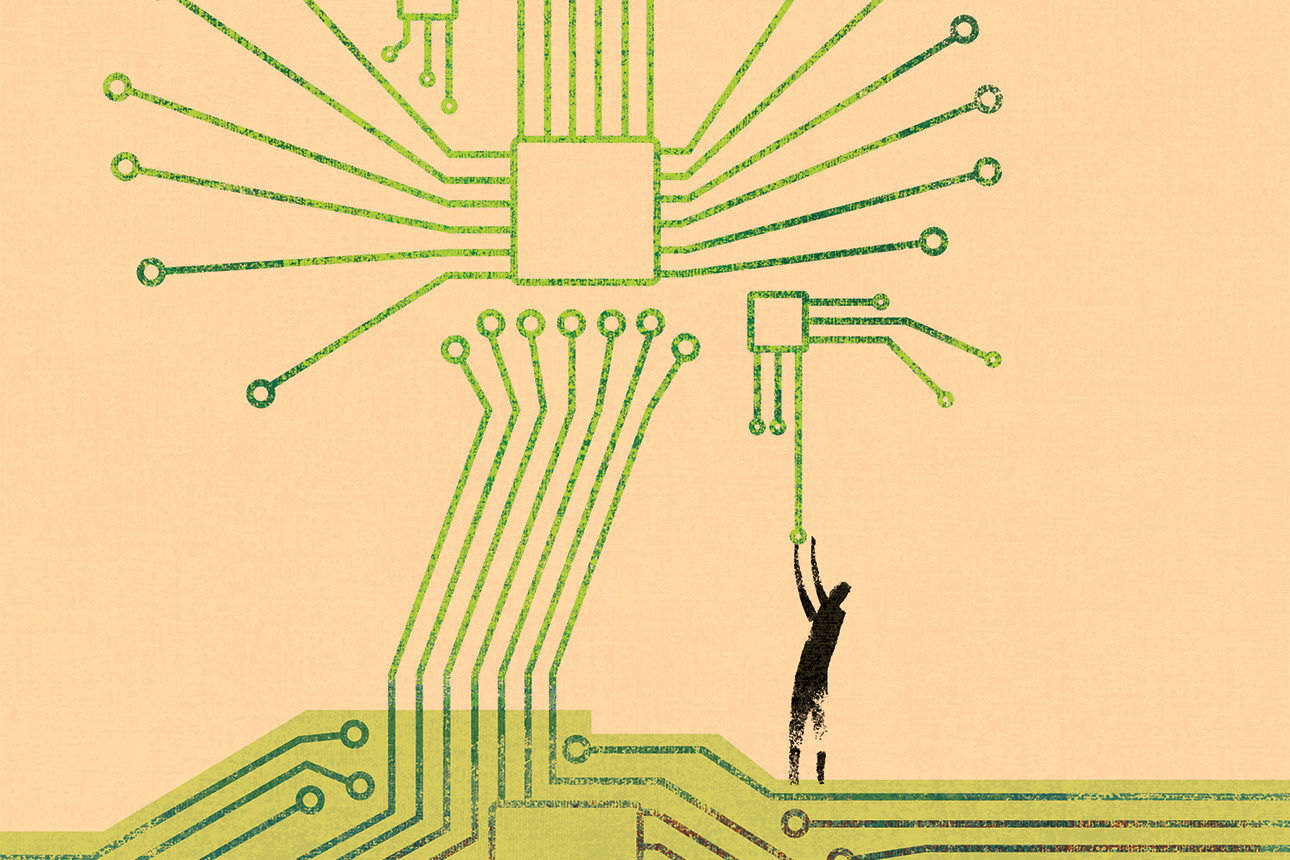
Image courtesy of Jing Jing Tsong/theispot.com
It was a matter of life and death. During the early onslaught of the COVID-19 pandemic, a hospital in Brescia, Italy, was running out of ventilator valves. The normal suppliers couldn’t meet the rapidly increasing demand for the parts, which were essential for keeping patients alive.1 So, in a moment of desperation, the hospital reached out to the local community for help. Isinnova, a company in Brescia with rapid prototyping capabilities, responded to the call. It reverse-engineered, prototyped, and then produced hundreds of 3D-printed valves that proved a good fit for the emergency. The same company then developed an innovative idea to transform a snorkeling mask into an emergency ventilator. Since these emergency ventilators were needed extensively all over Italy, Isinnova connected with the digital fabrication community to make the materials available to the local hospitals, reported Martina Ferracane, founder of FabLab Western Sicily. Thousands of adapters were produced and donated to hospitals across the region. A distributed ecosystem of digital fabrication facilities — some community-based fabrication labs, some commercial — had become an important part of the local supply chain to provide health care facilities with personal protective equipment (PPE), spare parts, and medical devices.
At a time when global supply chains and large-scale manufacturing are being revealed as fragile and vulnerable, the role played by digital fabrication technologies and local ecosystems gives us a glimpse into a future in which new forms of self-sufficient production can empower communities all across the world.
We define self-sufficient production as producing locally while connecting globally. We’ve seen how advances in digital fabrication have enabled globally connected local production ecosystems to design and deliver lifesaving products. Global connectivity enabled the open sharing of product designs, the identification of medical-grade raw materials, and innovative approaches for aligning designs with safety standards.
References (5)
1. Z. Kleinman, “Coronavirus: 3D Printers Save Hospital With Valves,” BBC, March 16, 2020, www.bbc.com; and D. Robitzki, “An Overwhelmed Italian Hospital Is 3D Printing Replacement Parts: Without the Extra Ventilator Valves, Some Patients Might Have Died,” NeoScope, March 16, 2020, https://futurism.com.
2. We highlighted places to look in our book, “Designing Reality: How to Survive and Thrive in the Third Digital Revolution” (New York: Basic Books, 2017).