What Happens When You Outsource Too Much?
With complex products such as automobiles, integration is a key element of performance. That means managers must understand which activities and competencies they can safely outsource and which they need to keep.
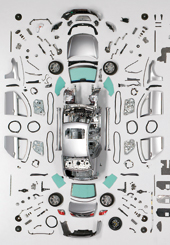
Image courtesy of Hyundai Mortor Co.
We live in an era in which business disaggregation is the norm. In industry after industry, managers have taken deliberate steps to separate their value chains and shift important activities and functions to outside suppliers. The outsourcing trend became increasingly visible during the 1990s, when companies such as IBM began to outsource not just manufacturing but also design activities. The trend reached its peak within the past decade, when even companies such as Boeing started outsourcing innovation activities. But what happens when companies become too dependent on outside suppliers and cede them too much control if they lack the same degree of understanding and awareness about how important product or service elements fit together and what’s necessary? Once management lets go of critical internal levers, how does it go about reestablishing them?
These questions arose during a multiyear research project examining supply strategy relating to new product development at a major European automotive company (see “About the Research”). In the late 1980s, the company — which we call Alpha — had direct supply relationships with more than 3,000 suppliers, most of them small companies. The suppliers were mostly involved in the production of components, and only to a limited extent in the design of components. In the early 1990s, however, management began shifting increasing amounts of design and engineering work to suppliers. That trend was hastened by the proliferation of electronics in cars, which was beyond the traditional competence base of automotive manufacturers. Although all companies shift activities to outside suppliers, Alpha pushed outsourcing even further. By the mid-1990s, Alpha began to outsource the design of complete systems, such as dashboards, seats and safety systems, to suppliers that had the ability to provide entire systems. (See “The Anatomy of an Auto.”)
The Leading Question
How can companies make the right decisions about outsourcing?
Findings
- Keep activities in-house that have direct impacts on product performance.
- Maintain control over activities that are highly interdependent with the technologies that impact on the performance of the overall product.
To senior management, outsourcing entire systems — including the design of those systems — seemed like the right direction. Similar supply arrangements were already common in other industries such as computers.
References (9)
1. A. Takeishi, “Bridging Inter- and Intra-Firm Boundaries: Management of Supplier Involvement in Automobile Product Development,” Strategic Management Journal 22, no. 5 (2001): 403-433.
2. The insight into the essential role of component-specific knowledge to design larger systems has been a central finding of research in the automotive industry. Interestingly, the same conclusion was also reached by research on innovation in the comic book industry. In this industry, Taylor and Greve found that combining knowledge requires a deep understanding of knowledge, rather than just information scanning or exposure. Their research hints at a reason why shadow engineering, listening posts and the monitoring of technological advances might not be sufficient to maintain component-specific knowledge at the cutting edge. See A. Takeishi, “Knowledge Partitioning in the Interfirm Division of Labor: The Case of Automotive Product Development,” Organization Science 13, no. 3 (2002): 321–338; Takeishi, “Bridging Inter- and Intra-Firm Boundaries”; and A. Taylor and H. Greve, “Superman or the Fantastic Four? Knowledge Combination and Experience in Innovative Teams,” Academy of Management Journal 49, no. 4 (2006): 723–740.
Comments (4)
vinay singh
Rushikesh K. Malaviya
Bill Young
Danny Pieters