How Workplace Safety Improves Performance
OSHA’s longest-serving administrator identifies safety approaches that work — and those that don’t.
Topics
Frontiers
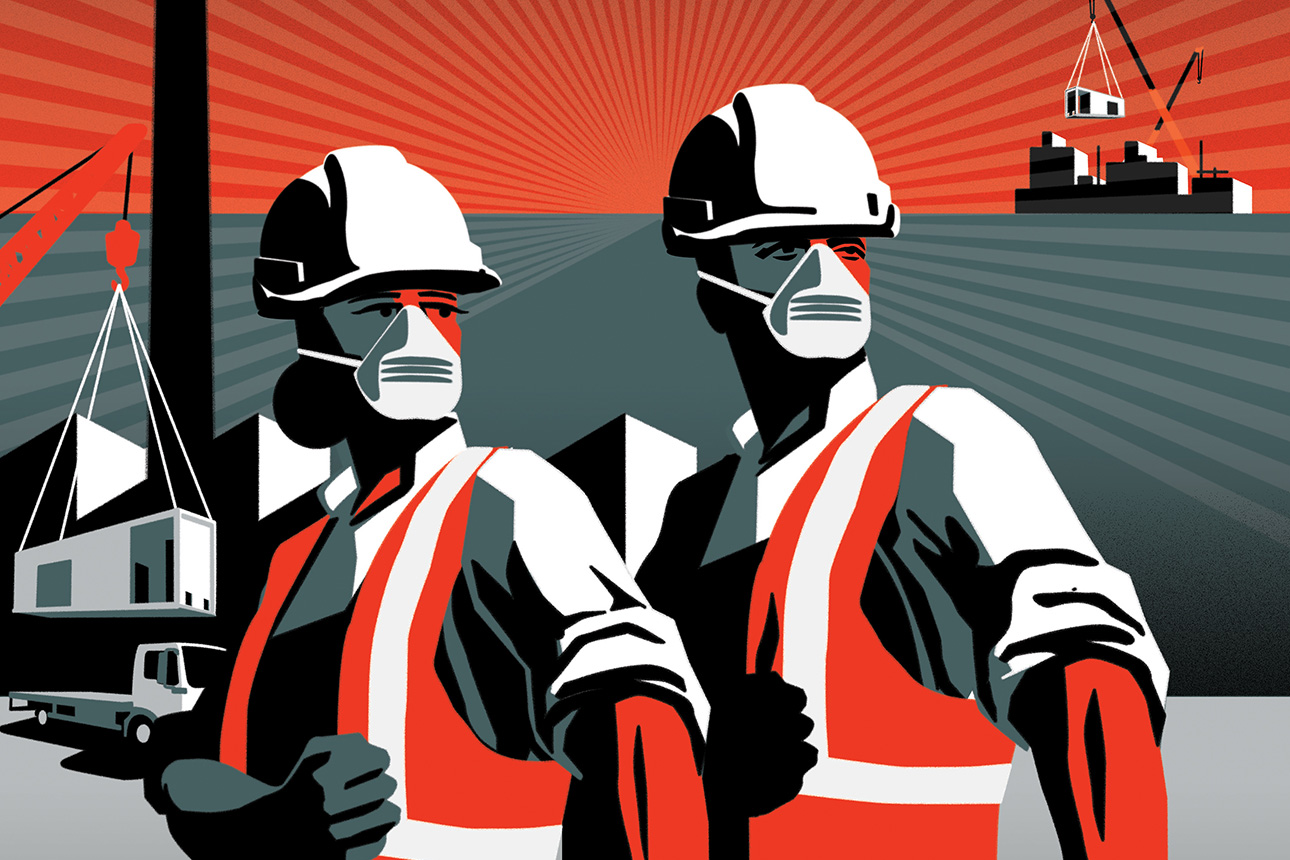
Neil Webb/theispot.com
Chasing lower labor costs, most of the United States’ toy and game companies have relocated production outside the country, primarily to Asia. One of the only remaining game manufacturing facilities in the U.S., in East Longmeadow, Massachusetts, was originally operated by Hasbro but is now run by Cartamundi, a Belgian company that manufactures products for Hasbro. It is a unionized factory in a state with high wage, tax, and energy costs.
The reason Hasbro didn’t follow the rest of the industry to Asia is that this factory runs much more efficiently than the ones that moved. Through a voluntary safety program under the umbrella of the Occupational Safety and Health Administration (OSHA), the plant’s managers and workers collaborate to find and fix safety hazards and, in doing so, have made the plant dramatically more productive. In fact, in 2017, Hasbro determined that it would be cost-effective to bring Play-Doh production back from Asia and manufacture it in Massachusetts.
I know this because I was the head of OSHA at the time and learned from executives at Hasbro that the safety program was a key reason behind the decision not to move the plant to Asia. I ran OSHA for more than seven years, from early in the Obama administration until Donald Trump took office in 2017, almost double the tenure of any other OSHA administrator.
In my decades of safety work in government and the private sector, I have seen very clearly that worker safety and operational excellence are inseparable, a conclusion that is supported by academic research. Businesses that have fully embraced worker safety produce a higher-quality product; have more productive, loyal workers; and, most importantly, experience fewer work injuries, which in turn greatly reduces the costs associated with such events.
The corporate leader who most influenced my thinking about workplace safety is Paul O’Neill, who was CEO of aluminum producer and processor Alcoa from 1987 to 1999. (It has since split into two companies.) Alcoa was struggling in terms of both profits and safety when O’Neill took over, and he soon made safety his primary focus. He instructed his managers to prioritize safety and set a goal of zero injuries in every one of Alcoa’s 342 facilities in 43 countries. Managers realized that to eliminate injuries, they had to understand and then tightly control the manufacturing process. Production costs went down, quality increased, and productivity skyrocketed. Six years later, sales were growing 15% annually, revenues had tripled, and earnings per share had risen more than 600%. In 2000, the year O’Neill retired, Alcoa was the best performer on the New York Stock Exchange.
The Consequences of Not Managing for Safety
Managing for safety can drive operational excellence, and failing to do so can threaten or even destroy an otherwise successful business.
In the 20th century, DuPont was one of the world’s leading chemical manufacturers and was deeply involved in worker protection efforts. DuPont’s expertise with safety even enabled it to sell safety consulting services to other companies. In more recent years, however, safety began to slip at DuPont facilities. In the years I ran OSHA, the company was not performing well; OSHA and Environmental Protection Agency inspections at several facilities found that the company’s commitment to operational excellence had broken down. Facing pressure from investors to reduce costs to increase short-term profits, DuPont let its safety program deteriorate even further.
One result was a tragic event at an insecticide manufacturing facility in LaPorte, Texas, where more than 20,000 pounds of an extremely toxic chemical were inadvertently released. When one worker was overcome by the fumes, three others rushed in to save their coworker without taking any safety precautions. All four were fatally asphyxiated by the gas.
It’s human nature to try to rescue someone in danger, but the last thing anyone wants is for the rescuers to become additional victims. Of course, the best protection is preventing a situation from happening in the first place. But workers in plants where there is the risk of chemical leaks need to be properly trained and equipped to safely rescue their colleagues.
It quickly became clear to our inspectors that DuPont’s fabled safety management program was a failure. OSHA issued DuPont a fine of $273,000 — a high penalty for OSHA but not for DuPont — and placed the entire company in its Severe Violator Enforcement Program, which meant more OSHA inspections of other DuPont facilities.
Soon afterward, DuPont was acquired by Dow Chemical, which then split the combined business into three smaller ones, one of which retained the name DuPont. From a worker safety perspective, this was a positive outcome, since Dow had a better safety operation than DuPont did before the merger.
Operational Excellence Through Safety
Safety organizations like OSHA and the National Safety Council issue reports that make the business case for safety by estimating the return on investment for safety programs. These reports show that the costs of serious injuries — including medical expenses and wage replacement, lost productivity, and hiring and training new employees — are higher than many corporate financial officers might estimate.
In my experience, however, the best leaders operate not on the basis of calculating the ROI on safety but from a recognition that by striving for operating excellence, they are making their companies safer, more productive, and more profitable.
Here are steps I recommend that leaders take to effectively implement safety management systems:
1. Take charge of your company’s safety program.
Safety comes from the top. Corporate leaders need to understand and be directly involved in addressing the safety and environmental risks that their workers and their facilities face. When executives are knowledgeable about and actively involved in their company’s safety program, including making appearances on the shop floor, workers perceive their employer’s commitment to their safety and well-being. It also provides executives with an opportunity to better understand the challenges and hazards workers experience and get their input on quality issues.
Many management experts consider the relocation of Boeing’s headquarters from Seattle to Chicago to be one of the underlying causes of the quality and safety issues recently seen in its aircraft. Former Boeing CEO Phil Condit’s rationale for the move — to keep corporate executives from being drawn into day-to-day business operations — seems particularly shortsighted, in retrospect.
2. Promote a safe operational culture, not a safety culture.
Workplace culture is a driver of workplace safety. Many CEOs will claim that their organization has a strong safety culture, but to me, that implies that safety is just one culture among many different ones that exist at the organization. Instead, safety must be the central component of the overall organizational culture.
Safety must be the central component of the overall organizational culture.
Safe companies that are committed to operational excellence are focused on safe operational culture, not safety culture. This goes beyond semantics: At these businesses, safety is integral to how the organization operates. Workers and managers are incentivized to prioritize safety in every aspect of their jobs.
3. Select and implement a safety and health management system.
Managing for safety requires a company to implement a systematic process to find and fix workplace hazards before workers are hurt. These safety and health management systems call for iterative, continual improvement on a number of dimensions, including management leadership, worker participation, hazard identification and assessment, hazard prevention and control, education and training, and program evaluation and improvement. Together, managers and workers plan how to identify and abate hazards, implement those plans, evaluate their successes and failures, and then start again.
The workings of successful safety management systems are not mysterious, and there is no need to invent your own. Among the most commonly used off-the-shelf systems are ANSI/ASSP Z10.0 and ISO 45001:2018. Some large corporations, like Chevron, Dow Chemical, and ExxonMobil, have developed their own safety management systems explicitly interwoven with operational excellence objectives.
4. Know your company’s safety performance.
At Alcoa, O’Neill required that all injuries anywhere in the company’s global operations be reported directly to him, and that its real-time global injury rate be posted publicly on the homepage of its website. By doing so, he sent a message that safety and production are intimately linked, and unsafe production is unacceptable.
It is vital to remember, though, that injury rates provide no information about the risk of catastrophic events. The day of the horrific Deepwater Horizon explosion in 2010, BP executives were on the drilling rig to present its workers with an award for their low injury rate.
Work injuries, while important to track and investigate, are lagging indicators. To evaluate safety progress, leaders must also select and track leading indicators — ones that are predictive of fatalities, serious injuries, or events that may have catastrophic consequences. Unfortunately, there is no single, universal indicator that evaluates a company’s safety management system, and getting a handle on a business’s safe operational culture is even more difficult. At OSHA, we would recommend that top managers select a small number of indicators to start and eventually add more as the program matured. The measures could involve hazard identification or abatement, training, incident investigations and time to close out of investigators’ recommendations, or a variety of other indicators.
Work injuries, while important to track and investigate, are lagging indicators.
One approach I recommend is encouraging workers to make “good observations,” defined by pharmaceutical maker Allergan as “safety observations that are communicated, documented, corrected, and help prevent incidents from occurring.” This is a useful way for workers to alert management to hazards while also promoting a continual focus on risk reduction. The speed with which the organization addresses serious hazards once they have been identified is another measure worth tracking.
5. Hold leaders and managers accountable.
Reward leaders and managers for superior safety and health performance. Bonuses should not be based on injury rates but on leading indicators that measure the functioning of a company’s safety and health management system.
Some companies reward managers for lowering injury rates. Not surprisingly, this approach encourages under-reporting. We saw many examples of managers using their authority to discourage injured workers from reporting their conditions. When injuries or close calls are not reported, no investigation into root causes can occur, and nothing is learned to prevent future injuries. It is an OSHA violation to retaliate against a worker for reporting an injury or an illness, or even to have a policy that discourages workers from reporting.
At Alcoa, O’Neill blunted this problem by giving his phone number out to workers and encouraging them to report unsafe conditions to him directly, as well as publicly penalizing managers who failed to report safety issues.
6. Plan for mistakes.
It is a myth that unsafe acts are the principal cause of incidents that result in injuries. While human error plays a role in many cases, it is rarely the only factor. While errors should be minimized, safety programs that primarily focus on preventing them are unlikely to succeed because some errors are inevitable — but injuries are not.
A key indicator of a successful operations system is that mistakes do not result in injuries or deaths. Systems need to be designed to account for human fallibility.
Some errors are inevitable — but injuries are not.
This lesson has been embraced by the commercial aviation industry. In 1998, air carriers, aircraft manufacturers, airline worker unions, and several government agencies voluntarily came together to form the Commercial Aviation Safety Team to develop and recommend safety improvements across the industry. This initiative has helped drive the fatal accident rate in commercial aviation to record lows.
Workplace hazards are becoming more significant, and employers face ever greater challenges to protect their employees. The frequency and intensity of natural calamities, infectious diseases, and extreme heat are all increasing due to the climate crisis.
Workers, especially younger ones, are increasingly unwilling to accept workplace hazards. Concerns about job safety have driven union organizing drives at Volkswagen and Mercedes, and they helped launch organizing efforts by baristas in Starbucks cafes across the country and workers at the Amazon fulfillment center in Staten Island, New York.
Every worker wants to be able to finish their shift and return to their family as healthy as when they started their day. Now is the moment for corporate leaders to recognize that taking real steps to protect their workers will have benefits for these employees and will make for better, more productive businesses.
Comment (1)
GLADYS VAZ